
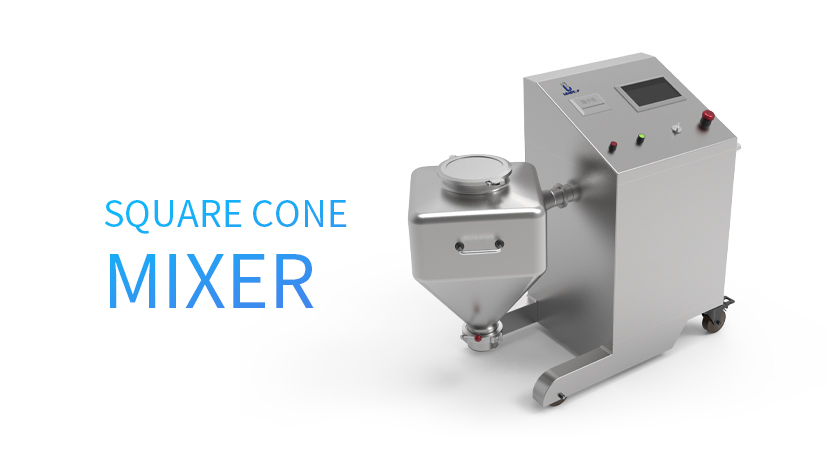
Not only is this dangerous for safety reasons, but you will also not be able to achieve that perfect blend. These static charges could potentially cause powders to clump or stick to the walls of the blender. The friction of two materials rubbing against each other causes the “triboelectric” phenomenon known as static charge. Challenge #3: Static Electricityīelieve it or not, static electricity can affect the process of mixing and unfortunately is often ignored. This type of blending uses micro and macro techniques which allow the material to flow freely inside the vessel, falling away from the walls.
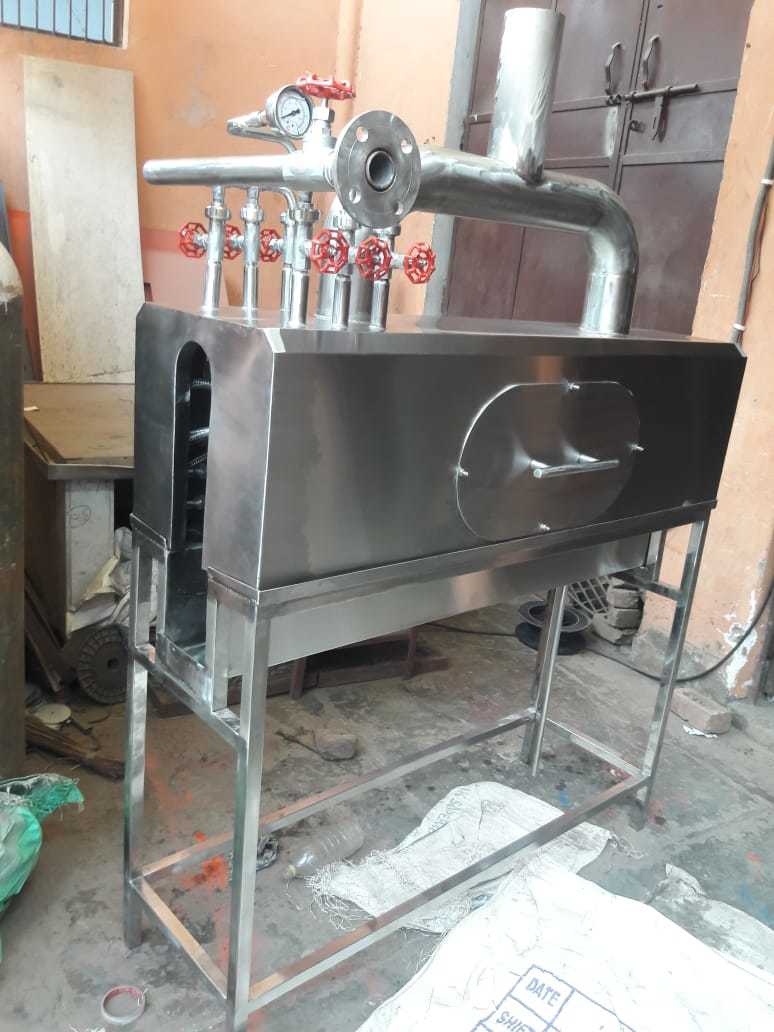
To address these complications, manufacturers have turned to tumble blending to eliminate dead spots. This positioning, however, can still leave material not being properly distributed and active ingredients are left concentrated in certain areas of the mix. Another solution manufactures have found is incorporating an intensifier bar in the vessel’s dead zones.
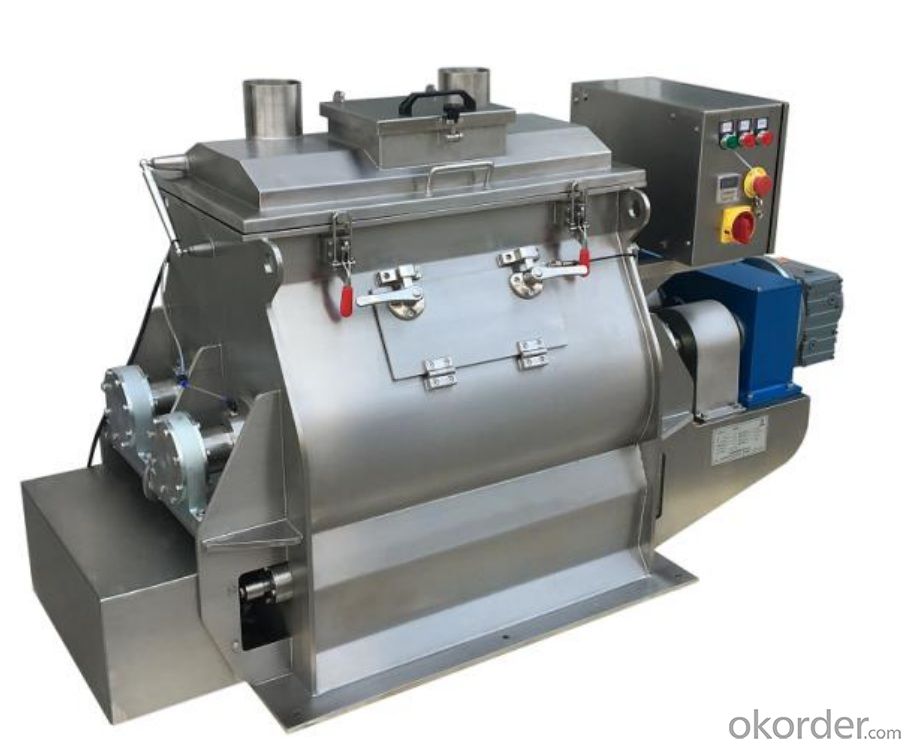
However, this method often leaves portions of the mix to receive more additives than others. These spots/zones are where material is left moving slower than the rest of the powders or remains static.Ī solution often recommended is for operators to empty the discharge area and manually reintroduce the stationary material back into the mixer. These limitations leave “dead spots” or better known as “dead zones” inside the blender. With traditional mixing equipment, these machines push material using blades or paddles, which sometimes limits the material’s movement within the vessel. Challenge #2: Overcoming Dead Zones Inside Your Blender Although this is an extreme example, the same concept is happening inside of a blender when particles are not uniform. It would be extremely difficult to mix these components evenly. Imagine trying to mix together star shaped blocks that weigh 5 lb with spheres that weigh 2 oz. When consideration is not given to a powder’s characteristics (shape, size, and density) the distribution of these active ingredients can be poor. Many of these blends and formulas are composed of as many as 40-50 components, some of which include trace amounts of powders (<1%) that vary in size and density. However, one of the challenges behind achieving a homogeneous blend is the disruption of trace amounts of ingredients. Powder blending can also be found in additive metals, chemicals, pigments, plastics, cosmetics, prosthetics, and much more.įor these products, especially for any GMP manufacturing, homogeneity is crucial to providing batch-to-batch consistency and repeatable results. Blending powders is a crucial step for a variety of products that include: pharmaceuticals, nutraceuticals, vitamins, mineral blends, and various foods.
